Steam cracking is a petrochemical process. Saturated long-chain hydrocarbons are broken down into smaller, often unsaturated ones in the presence of steam. Ethylene and propylene are the main products produced in the steamcracker and are among the most important molecules in the chemical industry. They are precursors for many products such as plastics (e.g., polyethylene, polypropylene), solvents, paints, vitamins, etc.
The cracking, i.e., the actual cleavage process, only takes a few fractions of a second. The different reaction conditions (feed composition, hydrocarbon-to-steam ratio, cracking temperature, furnace residence time) determine which products are obtained at which ratios. Increasing temperature, e.g., leads to the formation of primarily short-chain hydrocarbon compounds.
The workup and separation of the different fractions and products are very complex and pictured in a simplified scheme. Undesired fractions like alkanes can be recycled to the furnace. Fractions like methane that are not suited for cracking can be used to fire the furnaces thus delivering energy for the process. Pygas can be blended with other hydrocarbons as gasoline additive, or can be distilled to separate BTX (benzene, toluene, xylene).
click on picture to enlarge
Reference
- Heinz Zimmermann, Roland Walzl, Ethylene, in Ullmann’s Encyclopedia of Industrial Chemistry, Wiley-VCH, Weinheim, Germany, 2009. https://doi.org/10.1002/14356007.a10_045.pub3
Also of Interest
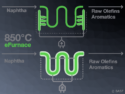
BASF, SABIC, and Linde begin construction; technology can reduce CO2 emissions by at least 90 % compared to conventional steam crackers
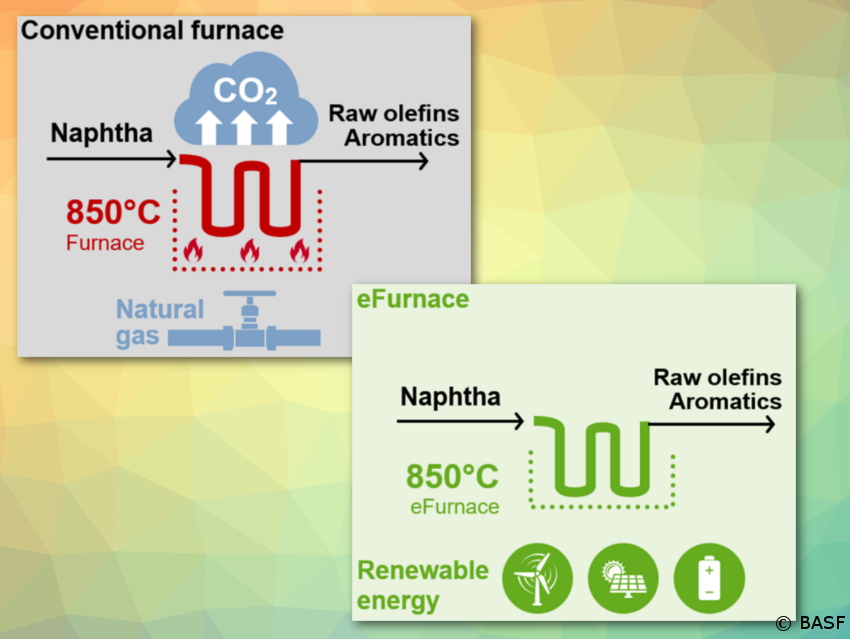
BASF, SABIC, and Linde join forces to demonstrate innovative concept to reduce CO2 emissions